ACCESS NOW: Distru’s Free Cannabis Cycle Count Template
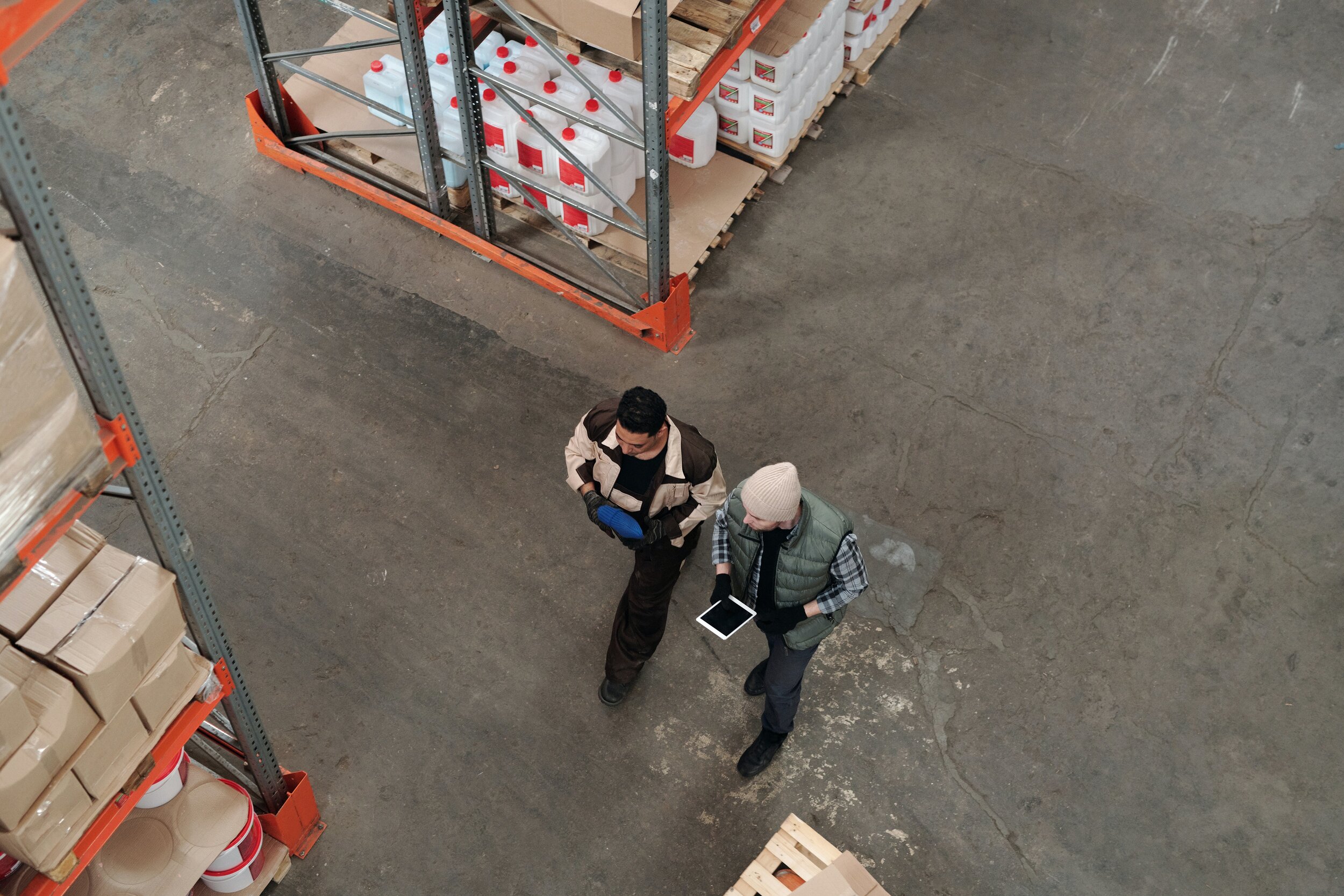
Auditing inventory is one of the most important aspects of inventory control in a cannabis operation. This process, also known as a ‘cycle count’, consists of checking the inventory level of each product in possession at the warehouse and recording it in a sheet, after which adjustments are made to reconcile physical inventory with the track and trace system and any cannabis software you may be using.
According to the regulations, a licensee is required to reconcile the physical inventory of cannabis goods at the licensed premises with the records in the California Cannabis Track-and-Trace system at least once every 30 calendar day, but for your business’ sake you will want to conduct these audits more often, as we discuss below.
In this post we propose a methodology that we have found beneficial to operators. There are different ways to conduct a cycle count, so feel free to adjust this process to suit your particular needs. This method entails getting an unbiased inventory count with notes, along with detailed explanations regarding any required adjustments. We’re confident that your audit team will find this beneficial so let’s get started.
.png)
Understanding Regulatory Guidelines
Let's start with the basics. Cannabis businesses across the United States must follow strict rules set by state regulatory bodies. While specific requirements can vary by state, there are some common threads. However, it's crucial to understand what constitutes a significant discrepancy in your inventory.
Before getting started, we highly recommend getting on the same page with your team on what discrepancies are. According to the regulations Section § 5034 of the BCC Guidelines:
Significant Discrepancy in Inventory. A determination by a licensee on whether a discrepancy in inventory is significant shall be made in accordance with the following:
(a) A significant discrepancy in inventory means a difference in actual inventory compared to records pertaining to inventory of at least 3 percent of the average monthly sales of the licensee.
(b) For the purposes of this section, average monthly sales shall be calculated by taking a per month average of the total sales for the previous 6 months. If the licensee has not been in operation for at least 6 months, only the months in which the licensee was operating shall be used in determining average monthly sales.
(c) For the purposes of this section, the licensee's acquisition price shall be used to determine the value of cannabis goods in a licensee's inventory. Authority: Section 26013, Business and Professions Code. Reference: Section 26070, Bureau of Cannabis Control Order of Adoption - 33 of 138 Business and Professions Code.
This definition of significant discrepancy is crucial for compliance. It provides a clear threshold for when discrepancies must be reported to authorities.
While this specific guideline is from California, many states have similar requirements. For instance:
- Most states require regular reconciliation between physical inventory and track-and-trace system records (like Metrc or BioTrack).
- The frequency of required reconciliations typically ranges from daily to monthly, depending on the state.
- Many states use a 30-day reconciliation period as a standard, similar to California's Bureau of Cannabis Control (BCC) requirement.
For example:
- In Colorado, the Marijuana Enforcement Division requires daily reconciliation for retail operations.
- Washington state mandates that licensees perform a full inventory reconciliation at least every 30 days.
- Oregon requires reconciliation at least once every 14 days.
Despite these varying official timelines, industry best practices suggest more frequent reconciliations. Daily or weekly inventory checks can help catch discrepancies early, preventing minor issues from becoming major problems.
Understanding these regulations and implementing a system to stay compliant is crucial for your cannabis business. Regular audits and accurate record-keeping are not just good business practices – they're essential for maintaining your license and avoiding penalties.
ACCESS NOW: Distru’s Free Cannabis Cycle Count Template
Cannabis Inventory Adjustment Reasons
Understanding the various reasons for inventory adjustments is crucial for accurate reporting and compliance. Let's break these down for both manufacturers and distributors.
.png)
Common Adjustment Reasons for Manufacturers
Cannabis Manufacturers, take note of these adjustment reasons:
- Enforcement Testing: When regulatory bodies take samples for compliance checks.
- Incorrect Quantity: For discrepancies between actual and recorded quantities.
- Mandated Destruction: When product must be destroyed as per regulatory requirements.
- Onsite Testing: For samples used in internal quality control processes.
- Over Pulled: When more product is used than initially recorded.
- Research & Development: For product used in creating new offerings or improving existing ones.
- Sample Tested: When samples are taken for third-party testing.
- Scale Variance: To account for minor discrepancies due to scale calibration.
- Spoilage: For products that have gone bad before their expiration.
- State-Authorized Adjustment: For adjustments specifically authorized by state regulators.
- Theft: When product goes missing due to suspected or confirmed theft.
- Under Pulled: When less product is used than initially recorded.
- Voluntary Surrender: For product voluntarily given up to authorities.
- Waste (Unusable Product): For product that becomes unusable during normal operations.
- Weight Change Due to Moisture: To account for weight fluctuations due to humidity.
Common Adjustment Reasons for Distributors
.png)
Cannabis Distributors, here are your key adjustment reasons:
- Damage (BCC): For products damaged during handling, storage, or transport.
- Incorrect Quantity: When actual quantities don't match recorded amounts.
- Mandated Destruction: For product that must be destroyed as per regulations.
- Over Pulled: When more product is distributed than initially recorded.
- Public Safety / Recall: For product recalled due to public safety concerns.
- QA Test Sample: For samples taken for quality assurance testing.
- Scale Variance: To account for minor discrepancies due to scale calibration.
- State-Authorized Adjustment: For adjustments specifically authorized by state regulators.
- Theft: When product goes missing due to suspected or confirmed theft.
- Under Pulled: When less product is distributed than initially recorded.
- Voluntary Surrender: For product voluntarily given up to authorities.
- Waste (Unusable Product): For product that becomes unusable during normal operations.
- Weight Change Due To Moisture: To account for weight fluctuations due to humidity.
Understanding these adjustment reasons is crucial for maintaining accurate inventory records and ensuring compliance with state regulations. When making adjustments in Metrc or your cannabis inventory management system, always choose the most appropriate reason and provide detailed notes to support your selection.
.png)
Our template includes a comprehensive list of these adjustment reasons, making it easier for you to categorize and document your inventory changes accurately.
Metrc Waste vs. Damage: Key Differences
Understanding the difference between 'waste' and 'damage' is crucial for accurate reporting:
- Waste Adjustments: Use 'waste' when product becomes unusable during normal business operations. Think of trim from harvested plants or oil left in extraction equipment.
- Damage Adjustments: 'Damage' is for when products are compromised unexpectedly. Dropped a box of edibles? That's damage.
With these adjustment reasons in mind, let's explore best practices for conducting cannabis inventory audits.
Reasons for Damage Adjustments in Metrc
Damage adjustments in Metrc can include:
- Accidental breakage: Oops! This covers those clumsy moments when products are accidentally dropped, crushed, or otherwise physically damaged. It could happen during handling, storage, or transport. For example, a jar of cannabis flower might be dropped and shatter, or vape cartridges could be crushed under heavier boxes.
- Environmental factors (like heat or moisture): Mother Nature can be tough on cannabis products. This category is for damage caused by environmental conditions. Extreme heat might melt edibles, excessive humidity could cause mold growth on flower, or freezing temperatures might compromise the integrity of liquid products. It's all about those external forces that can wreak havoc on your inventory.
- Packaging defects: Sometimes, it's not the product but the packaging that's the problem. This could include leaky containers, faulty seals, or packaging that doesn't adequately protect the product. For instance, a batch of pre-rolls might be damaged due to a manufacturing defect in the tubes they're stored in, or edibles could be exposed to air due to improper sealing.
.png)
Understanding these damage categories helps you accurately report issues in Metrc. It's not just about recording the damage – it's about identifying patterns that can help improve your processes. Maybe you need better packaging, improved environmental controls, or additional staff training on proper handling. By correctly categorizing damage, you're not just staying compliant – you're gathering valuable data to optimize your operations.
Best Practices for Cannabis Inventory Audits
Setting Up an Effective Audit Schedule
Weekly audits are the way to go. They help you catch issues early and keep your inventory tight. To make this process easier, take advantage of our free resource: Distru’s Free Cannabis Cycle Count Template
Conducting Blind Cycle Counts
Blind cycle counts are a powerful tool for maintaining inventory accuracy. In this process, staff members count products without knowing the expected quantities, eliminating unconscious bias. To conduct a blind count:
- Select a subset of inventory
- Provide counters with item information (but not quantities)
- Have them physically tally each item
- Compare results to system records
This method not only increases accuracy but also helps identify systemic issues in inventory management.
Investigating Discrepancies
When discrepancies arise between physical counts and system records, it's crucial to investigate calmly and thoroughly. Start by documenting the discrepancy and verifying it with a recount, preferably by a different team member. Then, review recent transactions, examine physical storage for misplaced items, and scrutinize your processes for potential issues.
Significant Discrepancy Thresholds and Reporting
In most states, a significant discrepancy is defined as a difference of 3% or more of your average monthly sales. If you hit this threshold, you must report it to your state's cannabis regulatory body and local law enforcement within 24 hours of discovery.
Now that we've covered best practices, let's walk through the step-by-step process of making adjustments in Metrc.
Preparing for Your Cannabis Inventory Audit
Align with Your Team on Inventory Conventions and Schedules
While the regulatory guidelines around discrepancies are there to help you stay within the boundaries of compliance, they are not there to help you run your business, which is why we propose doing more regular cycle counts. But before you do, it is vital to internally define what is important to your team. Is it just the dollar value? Is it also the units? Do discrepancies become more or less important for your business by category? By unit type?
For example, a small sample unit of a vape cart that’s missing is significantly less critical than a lb of flower that is missing, the latter being considerably more costly. Thus it’s important to have a nuanced view of your inventory instead of treating each package as equal to another due to innate differences.
Select your source for inventory data
There are two places you can get your inventory information:
- Metrc package export
- Cannabis software
Ultimately, you may need to compare your inventory count between Metrc and your cannabis software as well, although most software offers a way to reconcile with Metrc automatically, but in case it doesn’t then you will have to align the inventory in your software with the record of truth.
In this post we focus on an export from Metrc.
Prepare Adjustment Reasons for Your Team
Next, print and share the available Metrc Adjustment Reasons with your team (individual or multiple team members) who will be conducting the audit. This will help them better understand the available reasons and the type of notes needed to add to the package detail. Note that adjustment reasons for manufacturers and distributors differ.
Streamlining Adjustments with Distru's Metrc Integration
Distru makes Metrc adjustments a breeze. Its smart integration automatically categorizes adjustments, reducing errors and saving you time.
.png)
Setup your template for use
ACCESS NOW: Distru’s Free Cannabis Cycle Count Template
To carry out the cycle count, your team will need to enter data into a template. To make this process easier, we’ve created a free Cannabis Cycle Count Template in Google Sheets that you can access and copy for use in your own cycle count. As you do this, keep in mind that your business may have unique needs and the data you need may differ from another operation.
Once you are ready to start the cycle count, access the pre-configured template above, ensuring that the following column headers (at a minimum) are present:
- Name
- SKU
- Vendor
- Category
- Package Tag
- Active Quantity
- Pricing
Feel free to add columns depending on your situation. Next, hide the quantity column, which you can also lock for others to see. The reason for doing this is because you will want your auditor to do a blind cycle count where you remove any biases which we talk about in the next section. Check out this page for instructions on how to lock columns in Google Sheets. Once this is done, you will export your data from Metrc or your 3rd party software, add it to this template, and then lock the quantity column.
Once the template is set, duplicate the tab and share it with your team to use (do not share the original as it will need to be duplicated every time for use). Everyone has their own style or preferred way of doing the audit: some like to carry a tablet while others like to push their laptop in a cart around the warehouse. Either way shouldn’t be an issue and you can leave it to them to decide how they wish to do it.
One caveat to do this is that if you use an export from Metrc, you will see all Active packages, including any that might be reserved for sales in another part of your warehouse. Make sure to account for any inventory that may be reserved as it may not be with the rest of your inventory on the shelves depending on your order fulfillment process.
Automating Adjustments with Distru's Metrc Sync
Distru's Metrc sync feature revolutionizes the way cannabis businesses handle inventory adjustments. This powerful tool automatically pushes adjustment data from Distru directly to Metrc, eliminating the need for manual data entry and reducing the risk of human error.
While automation greatly simplifies the process, it's still crucial to regularly review your Metrc records to ensure everything is syncing correctly and your inventory remains accurate and compliant.
.png)
Selecting an inventory audit schedule and format
Once your adjustment reasons are printed and your data is exported, you need to select a cadence and process of conducting the cycle counts. Your audit team can conduct cycle counts either weekly, biweekly, or monthly. We recommend doing them weekly so that you are on top of any issues as they arise, such as missing inventory etc.
Next, select a process. You can audit your inventory in the following ways:
- By Metrc Category
- By Location
- By Subcategory
Auditing by Metrc Category would mean that you filter packages on your data export by a particular category such as Flower categories, and doing it by sub-category would be doing it by Flower (weight - each) for example. There isn’t actually a concept of a ‘sub-category’ in Metrc but you get the point. Your team would then check the quantity for each item per category, which should all be situated in proximity to each other in the warehouse.
Lastly, auditing by location would mean that you do it by shelf / area within the room (Metrc doesn’t offer this so you will have to access this in your cannabis software).
RELATED: 7 Metrc Mistakes Cannabis Distributors Make
Conducting the Inventory Audit
Start a blind cycle count
.png)
The purpose of doing a blind cycle count is to restrict the ability to make changes to the counted results. Blind counts are performed without knowledge of the quantity that is listed in the accounting records. If blind counts are not performed, the person performing the count may see the system quantity on the count sheet and simply match its count to the system quantity to avoid the hassle and additional time of investigating variances.
The audit process will depend on the format of the cycle count selected. In the case where the cycle count will be based on categories, the auditor will need to filter the products on the auditing worksheet by categories etc. In addition counting each product by category, it is critical that notes are tracked, especially for anything that looks suspicious: broken pieces, missing pieces, packages with 0 quantity and so on.
Investigate the outcome
After the completion of the cycle count, it’s time to dive in. You as the manager will need to review each line item after unhiding the columns, calculating discrepancies between what is showing in Metrc and what the audit team reported, and reading the notes. As per the regulations, use the following steps to determine if you have a significant discrepancy as you would need to report that within 24 hours of discovery:
- Determine the average monthly sales of the licensee by taking a per-month average of the total sales for the previous 6 months. If the licensee has not been in operation for at least 6 months, only the months in which the licensee was operating shall be used in determining average monthly sales. Take 3% of this average dollar sales number.
- Compare the value of actual inventory with the value listed in records pertaining to inventory. The licensee’s acquisition price shall be used to determine the value of cannabis goods in a licensee’s inventory. Take the difference between the dollar amount of the actual inventory value and the value listed in records pertaining to inventory.
- Is the number determined in Step 2 larger than the number determined in Step 1? If so, a significant discrepancy exists. If the number from Step 2 is less than the number from Step 1, a significant discrepancy does not exist. A licensee must notify the Bureau and local law enforcement within 24 hours of discovery of a significant discrepancy.
Next, you will want to look at all the discrepancies and figure out why they are occurring. Think of this as an investigative process where you connect with various members on your team and look for patterns to prevent these from happening in the future. Some adjustments such as moisture loss are unavoidable, but spoilage and theft should be at a very minimal.
Lastly, you can carry out your adjustments in your cannabis software, entering in the reason for each!
Conduct a Cannabis Inventory Adjustment Audit
In addition to your regular cycle count that you perform, we recommend you have your compliance officer conduct an adjustments audit. If you don’t have a compliance officer, you should get one for reasons described here. The adjustments report can be accessed from the reports section in your Metrc account and review it thoroughly (better to use the CSV than the PDF so that you can filter data in a way that is valuable for your operation).
Things to keep an eye out for:
- Adjustments without Notes
- Recurring Adjustments from specific users (why do they adjust so frequently?)
- Adjustment Date vs Package Date (infer reasoning for adjustments)
If there are any notable adjustments, investigate further to ensure that it is not a significant discrepancy, and if it was that it was reported to the BCC in a timely manner.
RELATED: Cannabis Naming Conventions Guide
Metrc item + strain audit (monthly)
As a bonus item, we suggest doing a monthly audit of your strains and items in Metrc to get rid of unused strains and items. There is a limitation to this wherein you cannot remove strains that have items with packages associated to them. Thus only when the packages are transferred out can you remove the strain.
In addition to removing unused strains, it is important to ensure your items follow a standardized naming convention and that the associated category and unit type is correct.
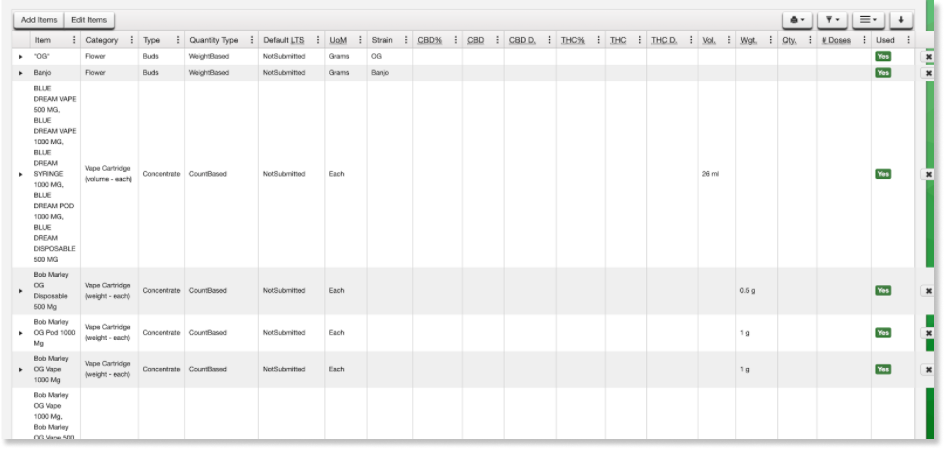
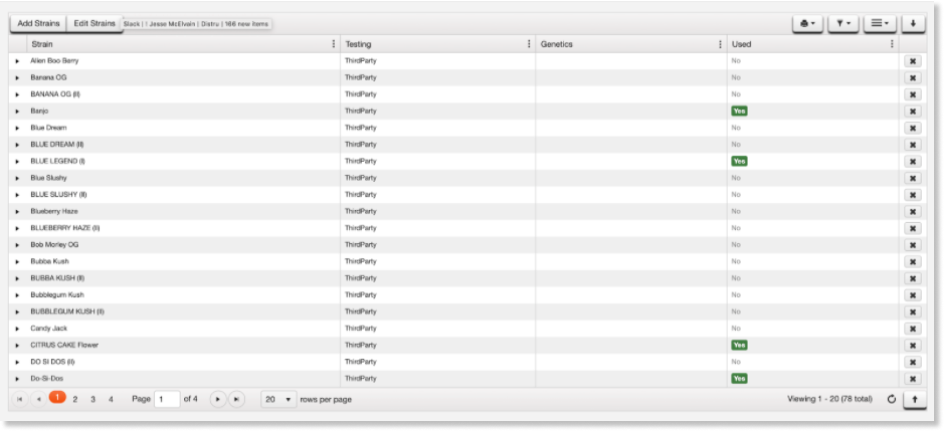
ACCESS NOW: Distru’s Free Cannabis Cycle Count Template
Automating Adjustments with Distru's Metrc Sync
Distru's Metrc sync feature revolutionizes the way cannabis businesses handle inventory adjustments. This powerful tool automatically pushes adjustment data from Distru directly to Metrc, eliminating the need for manual data entry and reducing the risk of human error.
While automation greatly simplifies the process, it's still crucial to regularly review your Metrc records to ensure everything is syncing correctly and your inventory remains accurate and compliant.
.png)