Important information: This guide is based on Massachusetts legislation but can serve as an example for businesses operating in states with similar cannabis laws. A special thank you to Lindsey Spurling of Green Analytics in Massachusetts for helping provide information in this article.
Although typically conducted at the end of the production process, just before products are packaged and distributed, cannabis testing is a crucial step for maintaining compliance. It's the final checkpoint to determine your cannabis products meet the standard for quality and safety.
The main players at this stage are cannabis testing labs, which carefully examine samples for cannabinoid content and contaminants to identify potential risks (pesticides, heavy metals, and microbial pathogens.)
Simply put, cannabis testing protects public health by ensuring products are safe for consumption and is key to compliance with strict industry regulations.
While testing is a standard practice, cannabis operators can make mistakes during the process, potentially leading to invalid or inaccurate results that can have serious consequences on products' quality and safety, as well as on their businesses' legal status and reputation.
In this guide, we'll go over the most common cannabis testing pitfalls and provide the best tips to avoid them. Read on!
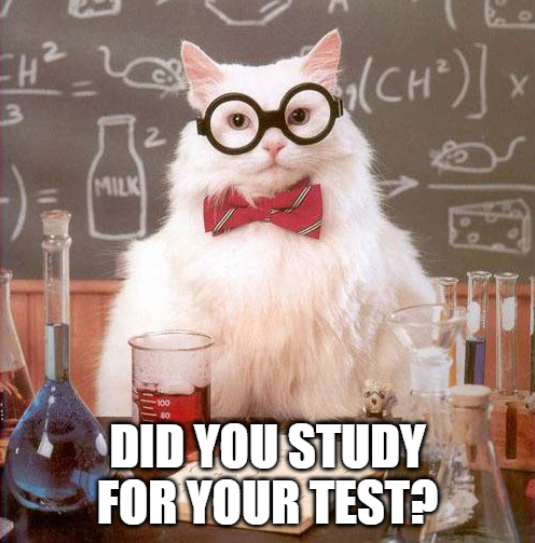
The Importance of Cannabis Testing
As mentioned above, cannabis testing is essential to ensure products are high quality and safe for consumption, whether they're used for medical or recreational purposes.
The Purpose of Cannabis Testing
Operators, especially processors and retailers, should test cannabis for metals and other contaminants, cannabinoid and terpene profiles, and other factors.
Testing cannabinoids helps assess products' dosage and effects, for example. This data can be used to ensure labels display the right information about their potency and potential side effects, which is crucial for proper use in any application and aids in ensuring operations adhere to strict cannabis-related regulations.
By testing cannabis for contaminants, operators can screen for substances that may be harmful to humans, such as heavy metals, pesticides, microbial pathogens (mold, bacteria, parasites, viruses, etc.), and residual solvents used in the extraction process.
Testing must be performed with the utmost care. Otherwise, results may be inaccurate and lead to contaminated or unsafe products, misleading potency claims, and incorrect label information, which can put consumers at risk and affect your business's success.
Cannabis Testing for Regulatory Compliance
Besides being used to determine if cannabis products are contaminant-free, high quality, and safe for consumption, testing is important to avoid regulatory violations.
Massachusetts requires all licensed cannabis operators, including Marijuana Establishments and Marijuana Treatment Centers, to perform rigorous testing for both medical and adult-use products.
These are the specific testing and analysis requirements in this state:
- Cannabinoid profile testing: Samples must go through quantitative and qualitative analysis to determine levels of cannabinoids (THC, CBD, etc.) and identify specific cannabinoids and their potential isomers. This information must be accurately displayed on labels.
- Contaminant testing: Cannabis products must also be tested for contaminants that may be potentially introduced at each production stage. For example, non-organic pesticides, metals, soil amendments, hydroponic products, and fungal and bacterial growth can contaminate products during cultivation. Finished cannabis products must be screened for these contaminants and mycotoxins that can be exacerbated during the finishing process, too.
- Environmental testing: In Massachusetts, the media where cannabis is grown (soil, water, and other cultivation inputs) must be tested to ensure it's contaminant-free.
Complying with such regulations can help you stay on the right side of the law to avoid potential penalties, such as fines and license revocations.
For more information on protocols for sampling and analysis of cannabis products and environmental media, refer to the following guides offered by the Massachusetts Cannabis Control Commission (CCC):
- Protocol for the Sampling and Analysis of Finished Marijuana Products and Marijuana Products for Marijuana Establishments, Medical Marijuana Treatment Centers, and Colocated Marijuana Operations
- Protocol for Sampling and Analysis of Environmental Media for Marijuana Establishments, Medical Marijuana Treatment Centers, and Colocated Marijuana Operations
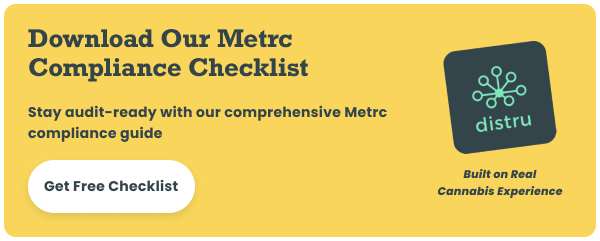
Selecting the Right Cannabis Testing Lab
To obtain accurate, reliable results on your products' quality and safety tests, you must choose the right cannabis testing lab, which must be accredited by the CCC and have verifiable experience in this field.
Accredited cannabis testing labs ensure that samples are screened against the strictest quality and safety standards, comply with all Massachusetts regulations, and provide accurate results in a timely manner, which can help you ensure your operations are legal and your products are ready for consumption.
Another important aspect to consider when choosing a cannabis testing lab is the services offered.
Key Tests in Cannabis Testing
Reputable cannabis testing labs typically offer multiple services, including the following:
Heavy Metal Testing
Cannabis products must undergo a screening process to identify potential heavy metals that may be absorbed through soil, water, and fertilizers used during cultivation, such as lead, arsenic, mercury, and cadmium.
The most common testing methods include Atomic Absorption Spectroscopy (AAS), Inductively Coupled Plasma Mass Spectrometry (ICP-MS), X-ray Fluorescence Spectroscopy (XRF), and Inductively Coupled Plasma Optical Emission Spectroscopy (ICP-OES).
It's important to test cannabis for metals for several reasons. First, heavy metals are toxic and can cause adverse health effects, including neurological damage and even cancer. If cannabis products are contaminated and consumed, they can pose serious risks to people.
If you don't comply with such regulations, your products can be recalled or banned from the market, and your business can be subject to harsh penalties.
Cannabinoid Profiling
Cannabis profile testing, also known as cannabis profiling, is performed to determine the specific cannabinoids present in a product, specifically assessing their type and concentrations.
These tests focus on cannabinoid and phytocannabinoids, including tetrahydrocannabinol (THC), cannabidiol (CBD), cannabigerol (CBG), and tetrahydrocannabivarin (THCV).
More often than not, liquid chromatography with ultraviolet (UV) detectors is used to identify and calculate the amount of major cannabinoids. For trace and minor cannabinoid analysis, many laboratories prefer mass spectrometry.
Liquid chromatography is conducted using high-performance liquid chromatography (HPLC) systems with UV detectors to separate the mixture of cannabinoids in a sample. UV light is then directed at separated compounds, which absorb it to a different extent depending on their concentration.
Mass spectrometry separates and measures the mass of the different molecules in a sample using LC/MS systems, which are similar to those mentioned above but are equipped with a mass spectrometer (MS) instead of UV light.
.png)
Understanding Metrc and Creating a Testing Batch
Metrc is the seed-to-sale tracking system mandated by the CCC, meaning all cannabis businesses in Massachusetts must use it. This software is designed to monitor cannabis products throughout the entire lifecycle, from cultivation to sale, which is key to maintaining accurate inventory records, controlling quality, and complying with state regulations.
How to Prepare a Sample Batch for Testing
All cannabis-containing products dispensed or sold by licensed businesses in Massachusetts must be sampled and subjected to rigorous testing. This applies to finished plant material, resin, concentrates (including vaporizer products), and marijuana-infused goods.
The nature and amounts or concentrations of contaminants and cannabinoids can vary throughout the production process, so it's important to perform the required tests at each stage. However, improper sampling methods, sample storage, and transportation can affect the results.
To avoid further contamination and obtain accurate results, you should complete the following steps:
- Take the sample: Using clean and sterile equipment, such as stainless steel spatulas, tweezers, or syringes, take a sample that accurately represents the entire batch. For flowers, for example, you can take a mix of buds, leaves, and stems from different locations within the batch. For edibles, on the other hand, it's best to take random samples of individual units within a batch.
- Store the sample: Cannabis samples should be carefully stored, typically in glass or food-grade plastic containers. Additionally, each should be properly labeled with the required information, including sample ID, product type, date and time of collection, batch number, and intended testing.
- Ensure proper storage conditions: Once in the container, samples should be stored in cool, dark, and dry places, avoiding exposure to direct sunlight, heat, and oxygen. Temperature fluctuations must be avoided, too. Some high volatile concentrates, such as live rosin, may require refrigeration.
- Transport samples: Cannabis samples should be carefully and securely packaged, preferably in insulated containers, for transportation, which must be done under Massachusetts regulations.
The Protocol for the Sampling and Analysis of Finished Marijuana Products and Marijuana Products for Marijuana Establishments, Medical Marijuana Treatment Centers, and Colocated Marijuana Operations offers more information on the requirements and due processes for taking samples for testing in Massachusetts.
Creating a Testing Batch in Metrc
In Massachusetts, sampling should be part of the seed-to-sale tracking process. That means samples must be logged in to Metrc.
Accurate reporting is essential for compliance and can help you ensure product safety. Therefore, you must follow state-specific guidelines for creating batches in Metrc Massachusetts and properly track them.
Here's a short step-by-step guide to help you:
- Go to the "Active" tab of the packages area on your Metrc license page.
- Find the Metrc package you pulled the test sample from and click on the item to select it.
- Click on the "Submit for Testing" button and fill in the blanks with the required details. The left side is where the new package information goes, and the right side is for the source package information.
- Review the source package listed for the #1 package to see if it's the one the sample was physically pulled from.
- Use the magnifying glass tool to find and select the corresponding package tag.
- Identify the package by clicking on the "Same Item" check box (the process is similar to repackaging). If you want to look up the item, use the magnifying glass tool next to the item rectangle.
- Enter the quantity (the amount pulled from the source package) and unit of measure (the same as the source package).
- In the "Required Testing" section, check the box that matches the product type that is being tested.
- Enter the package date by clicking "Today."
- Enter the amount taken from the source package that was sampled, which should be the same amount as the new package created.
- Double-check if the information entered is correct and click the "Submit for Testing" button.
If the package was created correctly, it should appear in the "Active" tab designated as "Test Sample" and with the "Submitted for Testing" status. After that, it should be put into a lab transfer manifest in Metrc to ensure it's properly monitored and accounted for as it moves to the cannabis testing lab.
Not in Massachusetts? Remember that the options you see when creating a testing batch in Metrc can vary depending on your state, so you may have to complete additional steps. However, the software's functionality is the same.
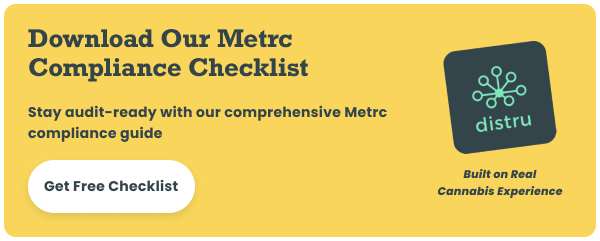
Key Cannabis Testing Compliance Pitfalls and How to Overcome Them
Although testing is a critical step in the cannabis production process, many operators make mistakes that can lead to costly delays, product recalls, and compliance issues. Below is more information on the most common ones and the best strategies to avoid them.
Selecting the Wrong Test Batch
Cannabis products are designed for multiple purposes and may be subject to different testing requirements based on their intended use. Those created for food-grade applications, such as edibles, undergo different testing processes than those manufactured for vape cartridges, for example.
Unfortunately, some operators select the wrong batch for the intended product use. This is one of the most common mistakes and can lead to multiple issues, such as incorrect labeling, harmful final products, and non-compliance.
To avoid this, you must ensure the test batch matches the product's intended use. Additionally, this information must be clearly and directly communicated to the cannabis testing lab.
Compliance Labeling
In Massachusetts, cannabis businesses must ensure products are properly labeled to maintain compliance. Labels must include accurate, up-to-date information, such as test results, production batch numbers, and expiration dates.
Some operators don't pay due attention to this requirement. Many even fail to ensure products are sold within a year of the testing date, which can result in a serious compliance violation.
If you're a cannabis operator, you should implement systems that allow you to track expiration dates correctly to ensure labels are updated with the latest test results and contain accurate details.
Handling Expired Products and Retesting
Massachusetts has specific and strict regulations for handling expired products. For instance, these items must be either disposed of or resubmitted for testing before going to market. Both processes must be performed according to state guidelines.
Expired items must be repackaged and transferred to the original processor or product manufacturer for retesting. Improper handling of these products can lead to unnecessary, costly losses. Therefore, you should follow the appropriate procedures in this scenario.
Reassigning Production Batches and Batch Conversion Mistakes
Another mistake that can lead to serious compliance issues is reassigning production batches without proper oversight.
Any changes made to the production batch can affect the accuracy of previous test results. If an error occurs, reporting will be incorrect, which can jeopardize compliance.
You should maintain accurate batch records throughout the entire process and minimize the need for reassignment. Additionally, it's essential to understand how these changes can impact compliance. Incorrectly assigning a package as a Production batch forces the retesting of a package, which can lead to unnecessary costs.
Insights on Testing for Specific Purposes
Products must undergo the right test for their intended use. For example, live rosin is subject to different parameters when tested for food-grade applications than when tested for vape cartridges.
You need to make sure the right tests are conducted for each product's intended use in order to accurately determine its potency and remain compliant. CCC regulations state exactly which tests are required for each product category. Thus, you should work closely with your chosen cannabis testing lab to avoid potential errors.
Navigating Metrc Compliance and Avoiding Loopholes
If you want to ensure you remain compliant when testing cannabis in Massachusetts, you should understand how Metrc works and the requirements related to this software.
As explained above, all cannabis businesses operating in this state are required to report in Metrc and ensure the data is accurate and up to date. So, learning how to use the system can help you avoid potential loopholes.
Failing to comply with Metrc reporting requirements can be catastrophic for cannabis operators, as it can result in severe penalties, such as fines or license revocations, and legal repercussions.
To avoid these potential mistakes, train your staff on how to use Metrc correctly and teach them the state-mandated procedures for complying with Massachusetts cannabis regulations.
.png)
Best Practices for Cannabis Operators
How you handle the testing process from start to finish can affect products' quality and your ability to remain compliant with state regulations. Below are best practices to help you ensure you get accurate results, guarantee safety, and meet strict legal requirements.
- Review and understand compliance bulletins on a regular basis to stay informed about regulatory updates, as some changes may affect testing requirements and procedures.
- Implement robust cannabis inventory management systems to properly track product expiration dates and ensure you correctly handle new and tested products. If possible, use innovative software with automation features to easily identify items approaching expiration and initiate required retesting or disposal in a timely manner.
- Maintain clear communication with cannabis testing labs to ensure the right tests are conducted according to products' intended use, as different regulations apply to each product form. Ensure laboratories are aware of these specifications to avoid errors that can lead to incorrect results.
- Educate your staff on compliance procedures, the legal requirements for safety and quality control, the most popular testing methods, and common pitfalls to avoid errors and potential compliance issues.
- Pay attention to the post-test process. After receiving results from the lab, compare product labels with test results to ensure information about potency, dosage, expiration dates, and other important details are correct. Keep detailed records of all test results, reports, and corrective actions taken.
- Handle retesting according to state-mandated regulations. Sometimes, cannabis products must be retested. This may be necessary in multiple scenarios, such as when the expiration date is approaching or when the initial test fails. If retesting is required, you must follow the steps outlined in Massachusetts regulations. More often than not, the process involves quarantining or isolating products in secure locations, disposing of or destroying affected items, or recalling them.
Final Thoughts
Cannabis testing is not only essential for compliance but also for your business's overall performance. Besides being required under Massachusetts regulations, this process can help ensure your products are high-quality and safe for customers, which can positively impact your reputation and drive sales.
If you understand the regulatory requirements, stay informed about evolving laws, keep detailed records of your operations, and handle the process correctly, testing your cannabis products can set your business up for success.
Use the tips mentioned above when taking, preparing, and storing samples, transferring them to cannabis testing labs, and reporting them on Metrc to uphold strict compliance standards, build a strong reputation in the industry, and grow in today's competitive marketplace.