As of January 1, 2018, all cannabis and cannabis products sold in California must be tested rigorously under state law. The regulations, according to California’s Bureau of Cannabis Control (BCC), require that all batches of cannabis products undergo testing by third-party laboratories that interrogate the samples for safety and dosing accuracy.
Testing requirements and acceptable limits of chemical and microbial contamination varies from compound to compound and can differ based on product type. Labs can test for potency, pesticides, microbiology, terpenes, heavy metals and more Certain tests have been required as of January 1st, 2018), with additional requirements added on July 1st, 2018, and the final set become mandatory for all products produced on or after December 31st, 2018. The following chart breaks this down in greater detail.
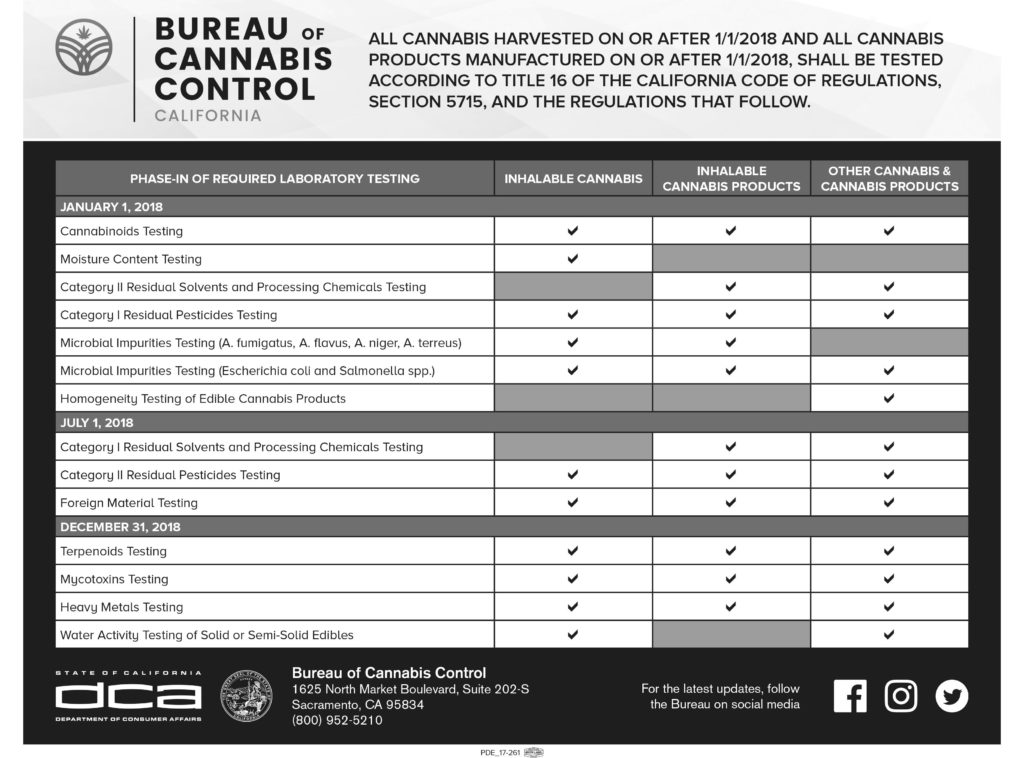
Licensed adult-use and/or medical cannabis distributors are legally required to facilitate compliance testing. Laboratories are required to develop and implement a chain-of-custody protocol to ensure accurate documentation of the transport, handling, storage, and destruction of cannabis samples.
Lab Requirements
- Labs must be independent and third-party. This means that a person who holds a license for a Cannabis testing lab cannot hold any other license. This is important for ensuring that there won't be any conflict of interest between labs and certain clients they test for.
- Labs must achieve ISO 17025 accreditation. (In most major countries, ISO/IEC 17025 is the standard for which most labs must hold accreditation in order to be deemed technically competent.) CW Analytical achieved this accreditation in August of 2016.
- Cannabis Laboratories must hold both a local permit, as well as a state license, and are regulated by the Bureau of Cannabis Control
-
Batch Selection
Distributors are not allowed to select their own samples; instead, distributors must work with a licensed testing laboratory who must come to their facility and conduct the compliance sampling process. The process is as follows:
- After taking physical possession of the batch(es) to be tested, the distributor is responsible for arranging for a laboratory employee to come to the distributor’s licensed premises to select a representative sample for laboratory testing.
- Only qualified employees from the lab must visit the distribution facility.
- The distributor is required to store the entirety of the batch (from harvest batches and cannabis product batches to be tested) until testing is done and it passes or fails.
- The distributor shall ensure that the batch size from which the sample is taken meets the requirements of this division; a batch may be over the size limit of the batch as set by the state, and would need to be split into multiple batches and tested separately.
- The lab sampler must have access to the entire batch (in an accessible location with no interference allowed) and will select 2 representative samples of the batch - a primary and a field duplicate.
- An employee of the distributor shall be physically present to observe the laboratory employee obtain the sample of cannabis goods for testing and shall ensure that the increments are taken from throughout the batch. However, the employee shall not assist the laboratory employee nor touch the cannabis goods or the sampling equipment while the laboratory employee is obtaining the sample.
- Both samples will be tested by the laboratory, but only the data from the primary sample will be reported to the client.
- The samples will be approximately the same weight (in the case of Cannabis flowers) or same number of units (in the case of pre-packaged Cannabis goods).
- The sampling shall be video recorded with the batch number stated at the beginning of the video and a visible time and date indication on the video recording footage. The video recordings shall be maintained for 180 days.
- After the sample has been selected, both the distributor and the laboratory employee shall sign and date the chain of custody form pursuant to section 5709 of the business code, attesting to the sample selection having occurred.
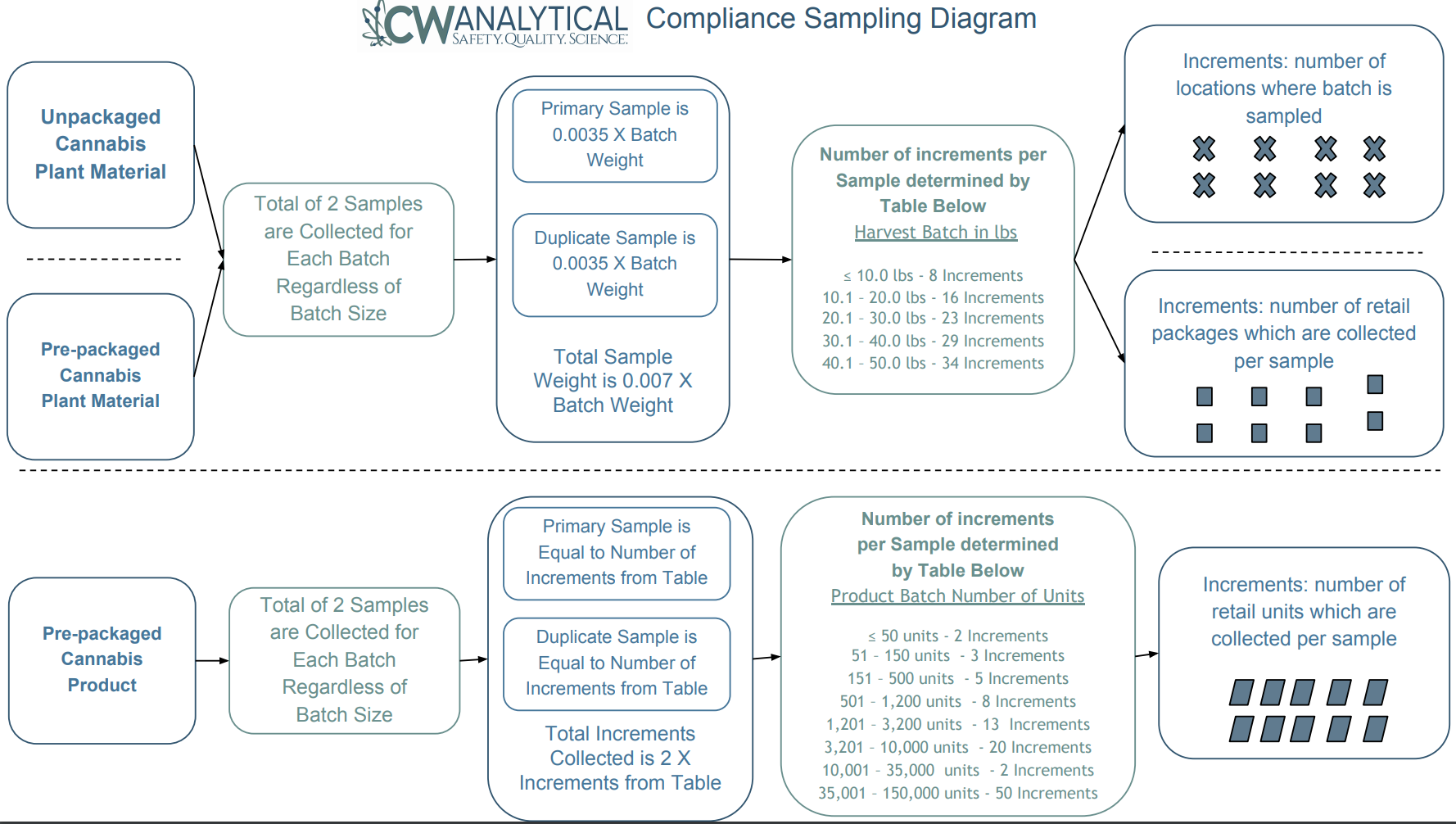
The image above, courtesy of CW Analytical, lays out how sampling works on a more granular level.
Post-Testing Quality Assurance Review
Once testing is complete, labs should destroy the sample unless more tests need to be conducted.
If test passes
- A sample “passes” a laboratory test when the sample meets specifications in chapter 6 of the Business and Professions Code.
- Distributor must obtain a certificate of analysis from the testing lab corresponding to the batch(es) being tested.
- The label on the cannabis goods is consistent with the certificate of analysis regarding cannabinoid content and contaminants required to be listed by law.
- Further duties around quality assurance are covered in the Quality Assurance section below.
If test fails
- A sample “fails” a laboratory test when the sample does not meet specifications of the Business and Professions Code.
- If a failed sample was collected from a batch and the batch could be remediated pursuant to section 5727 of the Business and Professions Code, a distributor may transport or arrange for the transportation of the batch to a manufacturer for remediation.
- A distributor shall destroy a batch that failed laboratory testing and cannot be remediated pursuant to section 5727 of the Business and Professions Code.
Please note that there are specific steps licensees can take, such as challenging failed lab tests, that we do not cover here.
Quality Assurance
The following are points related to QA which we cover more comprehensively in our labeling guide:
- A distributor may package, re-package, label, and re-label cannabis for retail sale
- A distributor shall not package, re-package, label, or re-label manufactured cannabis products except for when the distributor also holds a manufacturing license and is packaging, repackaging, labeling, or re-labeling its own manufactured cannabis products.
- Distributors may create pre-rolls as long as they are not infused with concentrates, which would require a manufacturing license
- Notwithstanding subsection (b) of this section, if it is determined during laboratory testing that a manufactured product is labeled with the incorrect amount of THC per package or serving but is within the THC limits for sale, the distributor may re-label the package with the accurate THC amount.
- When a distributor receives a certificate of analysis stating that the sample meets specifications required by law, the distributor shall ensure the following before transporting the cannabis goods to one or more retailers:
- The certificate of analysis the distributor received from the testing laboratory is the certificate of analysis that corresponds to the batch;
- The label on the cannabis goods is consistent with the certificate of analysis regarding cannabinoid content and contaminants required to be listed by law;
- The packaging complies with applicable packaging laws including, but not limited to, Business and Professions Code section 26120;
- The packaging is tamper evident. “Tamper evident” means a one-time-use seal is affixed to the opening of the package, allowing a person to recognize whether or not the package has been opened;
- The weight or count of the cannabis batch comports with that in the track and trace system. A distributor shall use scales as required by the Act;
All events up to this point will need to be entered into the track and trace system.
Track and Trace Requirements
- Once the sample is taken, a new package with its own tag is created by the distributor, and transferred to the lab via a manifest, which once RECEIVED by the lab, will deduct from the distributor’s inventory
- Labs do NOT need to create separate packages if the sample taken needs to be broken down into separate samples to test separately
- New packages only need to be created if the broken down samples will be taken to other labs
- Labs enter testing details into their LIMS (if there’s an API connection) or submit each type of test result carried out, along with pass/fail, inside track and trace system
- Samples are to be destroyed post-testing, which in METRC that would be a package adjustment and selecting ‘waste’
- Distributor and Producer would be able to see test results in track and trace system
- The results that will be available will only be based on what the state deems mandatory
Destruction and Waste Management
The proposed regulations specify that licensees must follow certain procedures in order to dispose of cannabis waste:
- Licensees must maintain a dedicated quarantine area, take precautions to secure the area, and make cannabis waste “unusable and unrecognizable” before removing it from the premises.
- This must be done by “grinding and incorporating the cannabis waste with non-consumable solid waste such that the resulting mixture is at least 50% non-cannabis waste.”
- Permitted types of non-consumable solid waste for these purposes include paper, plastic, cardboard, food waste, grease or other compostable oil waste, a compost activator, or soil.
- Cannabis waste must then be labeled with a bill of lading or shipping manifest that indicates product information and weight.
- Finally, it must be held in the quarantine location for at least 72 hours before being removed from the premises. All of this must be done on camera, and a separate surveillance camera with 30-day archive is required for the quarantine area.
Track and Trace Requirements
- If cannabis goods are being destroyed or disposed of, the licensee shall record in the track and trace system the following additional information:
- The name of the employee performing the destruction or disposal
- The reason for destruction or disposal
- The nname of the entity being used to collect and process cannabis waste, pursuant to section 5055
Qa Compliance Monitors
The BCC may conduct audits / reviews of distribution facilities by sending out a Quality Assurance Compliance Monitor. Details are as follows:
- The monitor is an employee or contractor for the Bureau.
- Quality assurance reviews are conducted randomly before product goes out for distribution to ensure that labeling is accurate and packaging conforms to requirements.
- The QA compliance monitor is to be given access to all records and test results of a licensee to conduct their reviews.
- All inspection records completed by a QA compliance monitor must be turned into the bureau.
- The QA monitor is also be responsible for verifying the accuracy of the tax payments collected under Sections 34011 and 34012 of the Revenue and Tax code.
- Access to the track and trace inputs and assumptions must be given to the QA compliance monitor, to ensure the accuracy of the data as well as that they match up to the tax payments.
Additional Comments
All of the aforementioned details do not prohibit a licensee from performing testing on the licensee’s premises for the purposes of quality assurance of the product in conjunction with reasonable business operations. Please note that the testing conducted on the licensee’s premises by the licensee does NOT meet the testing requirements pursuant to this division.
Distributors performing these services may collect a fee from the licensee for the services provided, in the case of an arms length transaction. The fee may include, but is not limited to, the costs incurred for laboratory testing. A distributor may also collect applicable state or local taxes and fees.
With the stricter monitoring of cannabis, consumers can feel more secure in buying products available on the market. This vast shift in regulations will increase the standards of all businesses, resulting in higher quality products. Companies that do not yet comply with the new rules must quickly organize to fit the new market policies so as not to risk losing their licenses and ultimately their market share in this burgeoning space.